Portalpacker
UNIPACK 2.0
Mit der Packmaschinenneuentwicklung UNIPACK 2.0 reagiert BMS auf die steigende Produkt- und Behältervielfalt im kleinen und mittleren Leistungsbereich. Im Vergleich zur Vorgängermaschine ist der neue Portalpacker deutlich leistungsstärker und ab sofort für alle „Pick and Place”-Anwendungen in der Brau-, Getränke-, Molkerei- und Lebensmittelindustrie geeignet.
Der UNIPACK 2.0 bietet alle Vorzüge der bewährten Portalbauweise von BMS wie höchste Flexibilität, kurze Umrüstzeiten oder eine große Investitionssicherheit aufgrund der Nachrüstbarkeit der Portalachse.
Weitere charakteristische Merkmale des UNIPACK 2.0 sind seine modulare Ausführung, sein durchgängiges Hygiene-Design sowie sein hinsichtlich Konstruktion und Bedienung optimierter Aufbau.

BMS Portalmaschine UNIPACK 2.0 Technologien im Überblick
Produktvorteile
- flexibel
- Parametrierbare Achsen
- Frei teachbare Positionen
- Auf das Produkt optimierte Packkurve
- Schnellverstellung der Anschläge
- zukunftsorientiert
- Offene Bauweise – „Rundum Sicht”
- Gute Reinigbarkeit
- Ergonomische Handhabung bei Kopf und Garnituren Wechsel durch optionalem Garniturenmagazin Achsen
Flaschentisch
- Integrierter Rüttler und Vollzähligkeitskontrolle
- Überleitblech zwischen Behältertransport und Flaschentisch
- Behältertransport je nach Aufgabenstellung mittels Scharnierbandkette aus Stahl oder Kunststoff bzw. Mattenkette
Gebindetransport
- Integrierte Einlauf- und Gebindestopper
- Gebindetransport mit Stahl-Scharnierbandkette
- Optimierte Geländer
Packtulpen
Je nach Sortiment optimierte Langzeit Packtulpen
- Packtulpe mit Greiffinger
- Packtulpe mit aufblasbarer Manschette
- Packtulpen für PET
- Packtulpen für Bügelflaschen
- Packtulpe für enge Räume
- Selbst entwickelter Vakuumgreifer
- Sonderpacktulpen
Greiferköpfe
- Starre und axial verschiebbare Greiferköpfe
- Individual verschiebbare Greiferköpfe für individuelles Gebinde
- Greiferköpfe für Karton
- Umpackgreiferköpfe für Karton
Zusatzeinrichtungen
- Automatische Etikettenausrichtung
- Automatische Bügelausdrehung
- Vollkastenkontrolle
Packer with Delta Robots
FlexLine
Optimise sticks handling with the A+F FlexLine, our packer with Delta robots and 3D movements. You want to convert existing systems? This can be done quickly and reliably using accurate format kits. Benefit from reduced operating costs thanks to low-maintenance design – and ensure a reliable and gentle pickup an placement of your sticks, including reject ejection.
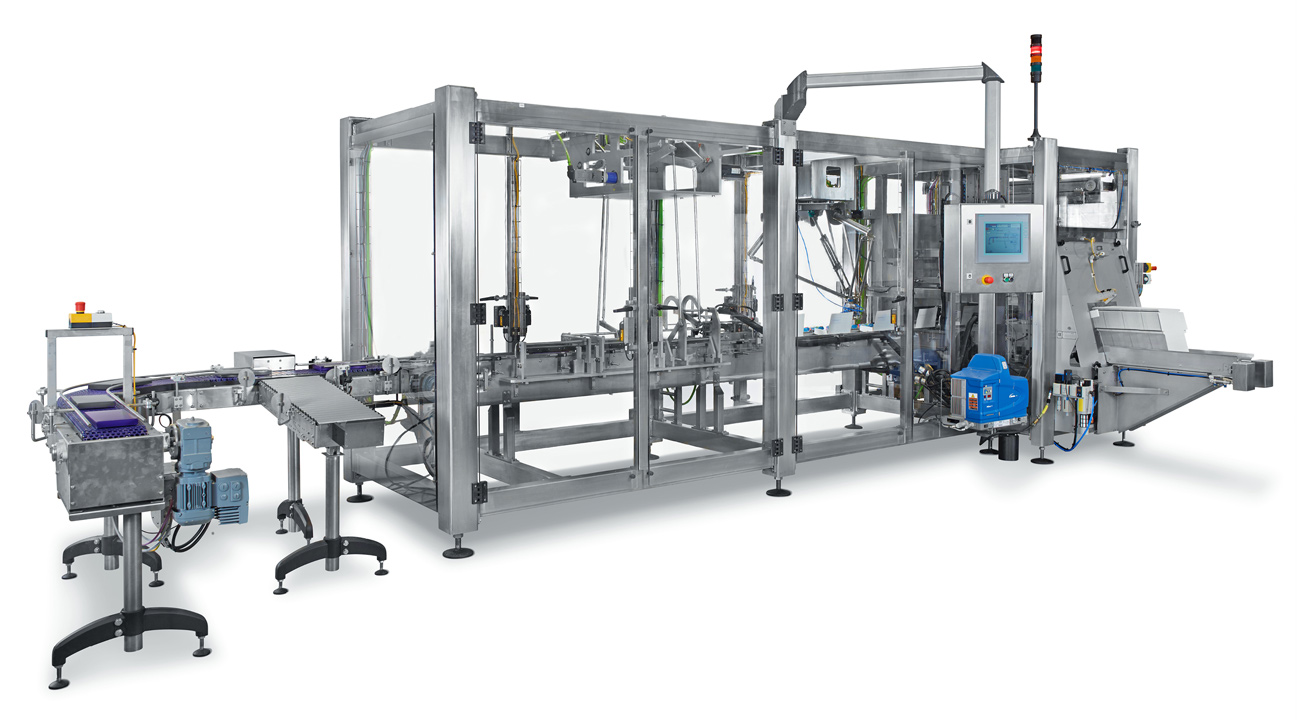
A+F FlexLine in detail
Benefits
- Quick, reliable conversion through the use of precisely fitting format sets
- Low operating costs due to high-quality, low-maintenance design
- Before delivery, the A+F FlexiLine is run in with original sample material and undergoes a documented final inspection
Technical details
- Sticks packed in foil 4 x individually cut or 2 x uncut as groups of 2 contiguously or 1 x uncut as a group of 4 contiguously
- Stick parameters: 235mm x 45mm x 10mm (LxWxH); 12g
- Capacity: 12,000 sticks / hour with flexpicker Cycle time: 1.2 seconds
- Control: Schneider Electric
Schneider Electric servo motors
HMI Siemens TP 1200 Comfort
Functional description
- Stick feeding 4 x individually, 2 x as a group of 2 or 1 x as a group of 4 together, on transport system technology
- Recognition of the sticks in the A+F system by sensors
- Ejection of faulty sticks in case of signal from the filling machine
- Picking up the sticks and placing them in stacking tray 1
Stacking the sticks according to the packing format - Procedure stacking chute 1
Removal of the stacked sticks from the stacking chute and placement in the prefolded wraparound carton
While stacking chute 1 is in the removal position in front of the carton line, stacking chute 2 is loaded by the flexpicker
Pick+Place Packer
TwinLine
Create a multifunctional basic module for a variety of packaging tasks. You are looking for an all-rounder with the ideal mix of speed and load capacity? Then the twin-axis robot A+F TwinLine offers you the perfect basis for any application in the packaging industry. The module can be adapted to your specific task at any time by means of servo-pushers, suction grippers or mechanical grippers and also using additional turning and tilting functions. Use the easy-to-operate A+F TwinLine optionally for collation of the primary products, for sorting cups or beverage bottles or for a different pick-and-place task.
By the way: Thanks to drive struts made of lightweight CFRP and the installed servo technology, fast reactions and short cycles with loads of up to 63 kg can be realised without difficulty.
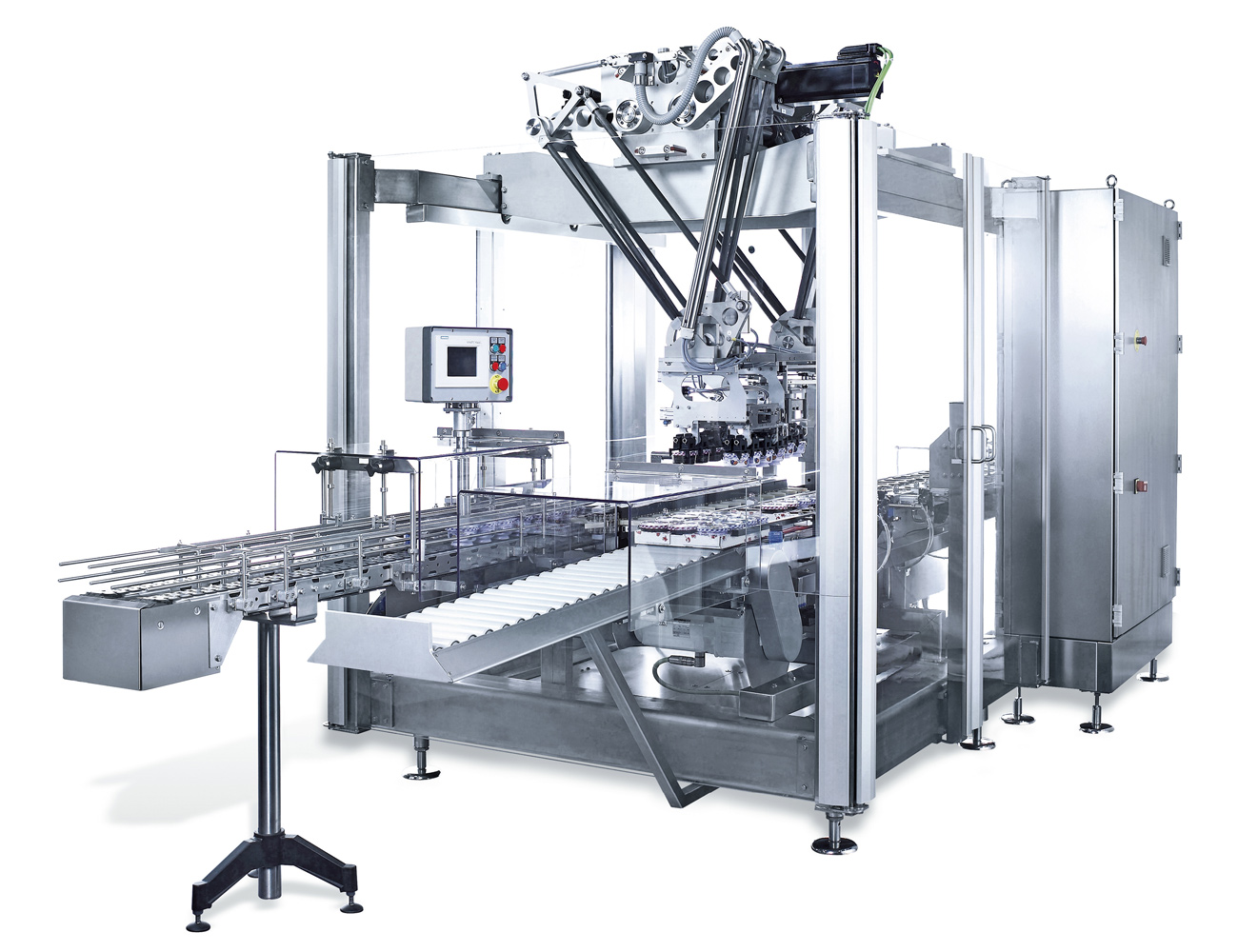
A+F TwinLine in detail
Benefits
- Unique combination of short reaction time, fast motion sequences and high payload up to 63kg with a high positioning accuracy
- Innovative technology in lightweight construction and servo technology
- Application- and customer-specific designs of the product infeed and the carton line as well as application-specific design with servo-driven pusher, suction gripper or mechanical gripper
- Multiple uses - pre-grouping of primary products, repacking or sorting of products as well as insertion of products into product carriers, trays or perforated trays
- Low production costs due to high-quality, low-maintenance design
- Ergonomic design for optimum operability and fast format changeover in less than 10 minutes
Technical details
- Control:
TwinLine MIN: Schneider Electric, Allen Bradley
TwinLine ST: Schneider Electric, Allen Bradley
TwinLine MAX: Schneider Electric, Allen Bradley - Weight capacity:
TwinLine MIN: 10 kg
TwinLine ST: 25 kg
TwinLine MAX: 63 kg - Reach A:
TwinLine MIN: 630 x 320 mm
TwinLine ST: 1080 x 400 mm
TwinLine MAX: 1350 x 500 mm - Range B:
TwinLine MIN: 500 x 254 mm
TwinLine ST: 800 x 400 mm
TwinLine MAX: 1070 x 500 mm
Applications
- Grouping, handling and aligning products
- Sorting products, e.g. cups or bottles
- Positioning products in product carriers or loading products into secondary or tertiary packaging
- Containers: pre-formed boxes, open trays, perforated trays, trays with lids.
Options
- Exchange tools for quick format change
- Connection of the TwinLine to upstream and downstream equipment in an extremely compact configuration
- Customised and application-specific configurations and technical solutions
- Optional integration of an optical detection system for product position and orientation detection
- Systems for detecting product contamination and rejection in terms of integrated quality assurance
- Intelligent palletising solutions
Assortment Packer
SortPacker
Switch from time and cost-consuming manual sorting to a flexible assortment packing. You would like to vary the packing of your cases? With the A+F SortPacker you have an assortment packer of modular design that can be extended to suit any type of sorting at any time. If desired, it can be extended to include a A+F SetLine, aligned to multi-layer packaging and optionally equipped with a changeover system for the grippers. Straightforward, fast and variable packing of cases – that’s what the A+F SortPacker stands for.
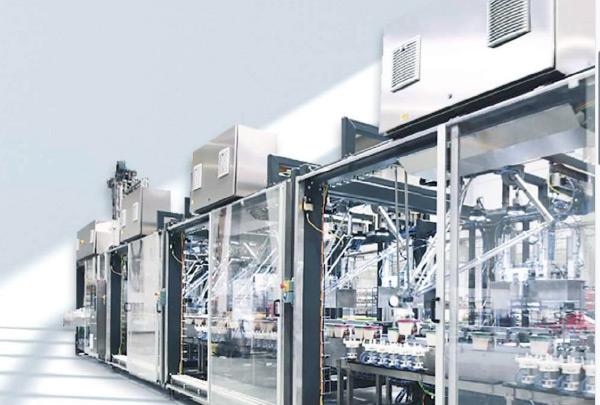
A+F SortPacker in detail
Benefits
- Low space requirement due to the compact design
- modular machine concept allows adaptation to customer-specific requirements
- central machine operation
- Flexibility in the combination of grades and in the event of format changes
Technical details
- Performance: Clock rate between 30-40 cycles/min.
- Products: Cups, bottles, glasses, etc.
- Container types: Crates, trays, plastic crates, goods carriers.
- Electrical connection: 230/400V, 50 Hz, approx. XX KVA
- Compressed air connection: R1″, 6 bar
- Module dimensions: approx. 4,500 x 2,300 (without feed lanes) x 2,700 (LxWxH)
Applications
- Products: Cups, bottles, glasses and much more.
- Containers: crates, trays, plastic boxes, product carriers
Options
- Separate case supply (erector) can be connected upstream of the assortment packer. This can be done directly or via an additional trans system
- Completion with corresponding labelling, inspection or reading systems
- Completion with downstream machines from the A+F portfolio, e.g. packaging systems, carton lidding machines, web inserters, etc.
Wrap-Around-Packers
Our 3 all-rounders: CompactLine, ModuLine, ContiFlex
With the A+F CompactLine butter packer, you can pack up to 150 wrapped butter packets in wrap-around cartons. Adaptable to other formats at any time.
With the A+F ModulLine cycle-controlled packer, you use one resource for all product grouping, loading and sealing tasks. Modular in design and individually adaptable.
With the A+F ContiFlex bottle packer, you handle up to 60 packs per minute. Simple format adjustment for carton line included.
CompactLine
Pack up to 150 wrapped butter blocks in wrap-around cartons using our newly developed A+F CompactLine butter packer.You want to change the format? Simply use the available format kits which allow a fast changeover of the machine. Single-row or double-row pack formats of different layer heights are thus possible at any time.
Incidentally: The A+F CompactLine can be connected to any wrapping machine of the mid-range performance class.
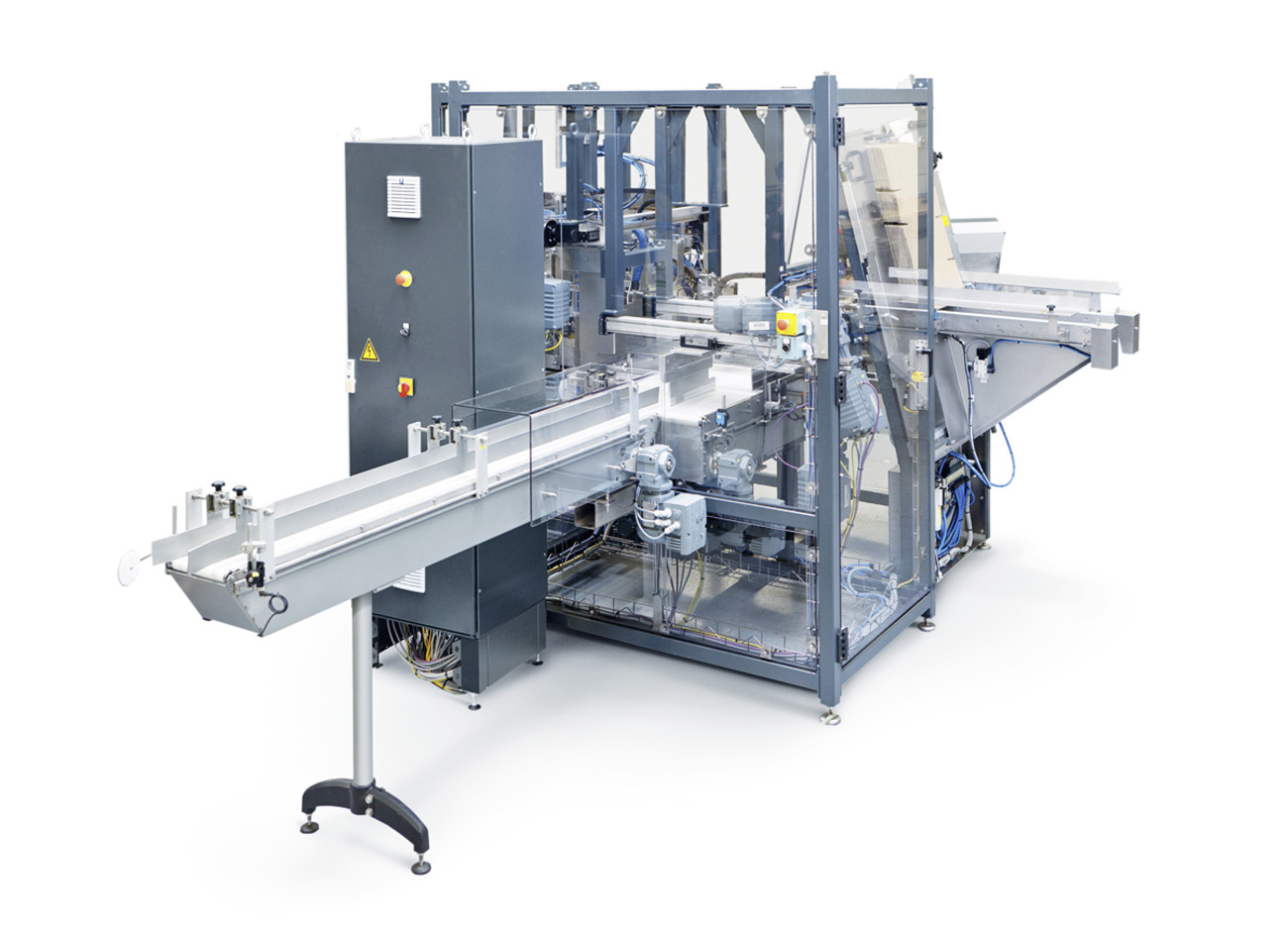
A+F CompactLine in detail
Benefits
- Modular design
- Simple operability
- Space saving design
- Short installation times
- High availability
Technical details
- Product supply rate: max. 150 products/min.
- Performance: max. 10 cases/min., depending on product type and shape
- Case size range: min. 230 × 100 × 64 mm (footprint L × W × H), max. 460 × 313 × 220 mm
- Product size range: Packing in one row: min. 100 x 30 x 16 mm – max. 200 x 105 x 100 mm (L x W x H, wrapped butter packs)
Packing in two rows: min. 50 x 30 x 16 mm – max. 150 x 105 x 100 mm (L x W x H, wrapped butter packs) - Weight: 50 to 1000 g
Application
- Open Trays
- Wrap-Around Trays
- Shoulder trays and Displays
Options
- Connection to upstream wrapping machine
- Conveying lines
- Complete palletizing solutions
ModuLine
Handle all conceivable product and pack types using our universal packer A+F ModulLine. You are looking for a machine for all steps in the packaging process? Thanks to its modular design this packer can accomplish every task – collation into the desired packing configurations, loading into erected cases and any closing applications, all in one machine. With over 1000 installations worldwide and an output of up to 30 packs/minute the A+F ModulLine is the true classic among packaging machines.
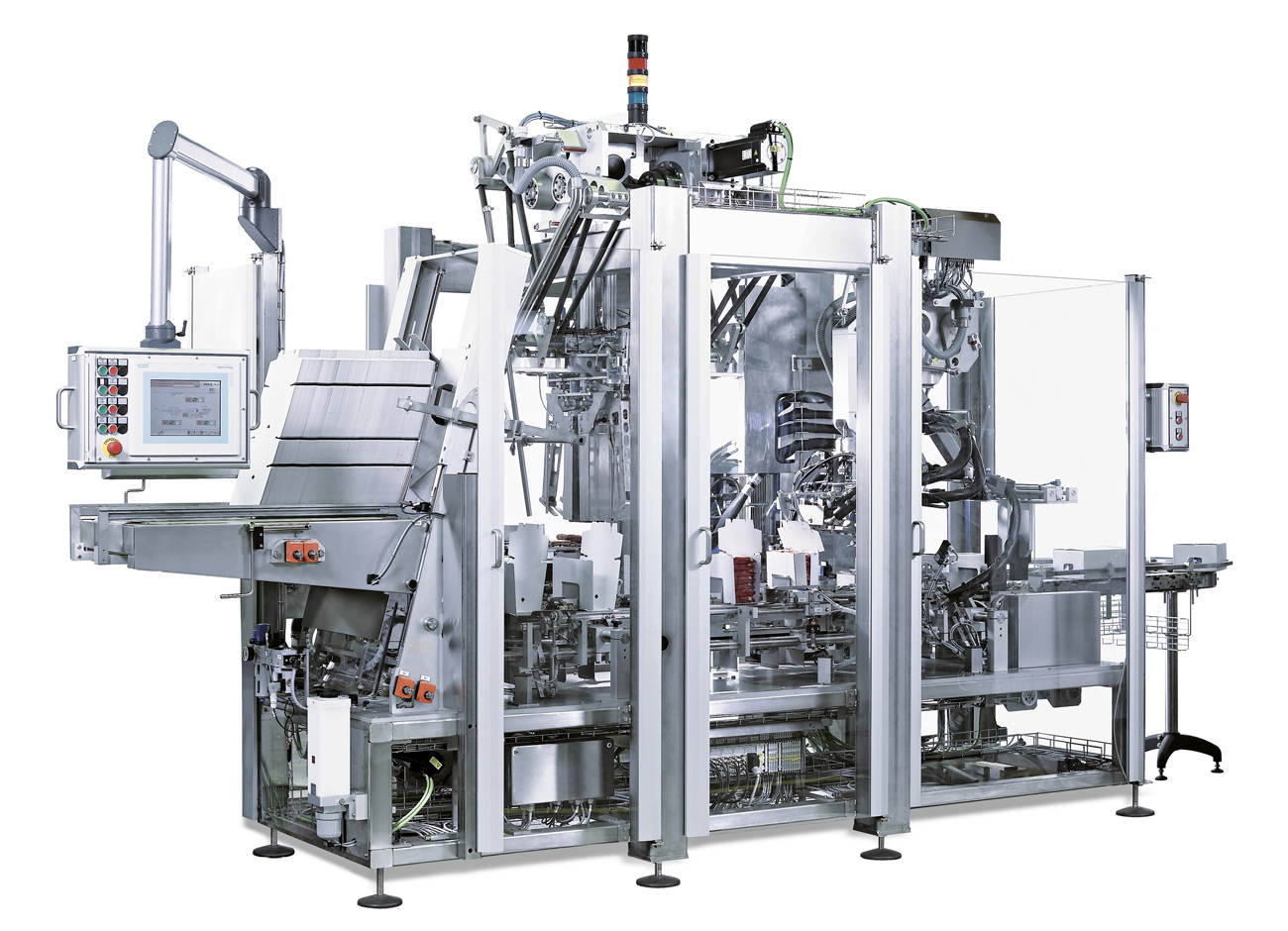
A+F ModuLine in detail
Benefits
- Maximum flexibility coupled with high net production
- Modular carton line and packable product grouping and modular packing cell in application-specific design with servo-driven pusher, 2-axis module or gantry module
- Wide range of product types and pack types that can be processed - with single-row, multi-row, single- or multi-layer, upright, horizontal or stacked product grouping
- Extremely compact design with a variety of set-up options (L, U, Z and mirrored designs) for optimisation of space requirements
- Low production costs due to high-quality, low-maintenance design
- High format and positioning accuracy
- Ergonomic design for optimal operability and fast format changeover in less than 10 minutes
Technical details
- Type of tray/case: open trays, wrap-around trays and cases, trays with attached or separate lids, shelf-ready display trays
- Speed: Max. 30 trays/min – depending on products and package dimensions
- Tray/case size: Infinitely adjustable
Length: 120 - 460 mm (standard) - max. 610 mm on request
Width: 90 - 300 mm (in transport direction) - max. 410 mm on request
Height: 80 - 300 mm
Applications
- Packaging of butter, margarine and other edible fats
- Packaging of yoghurt cups (single cups, cup set, multi-chamber cups)
- Packaging of food in very small portions
- Packaging of jars, bottles and cans
- Packaging of small packages, e.g. tea, cereals, etc.
- Packaging of beverage cartons and PET bottles
- Packaging: open trays, wrap-around trays, trays with lids as well as display trays
Options
- Carton line prepared for inserting perforated plates to fix cups
- Exchange tools for TwinLine 2-axis robot or gantry module to enable fast format changeover
- Connection of the ModuLine to upstream or downstream lines in an extremely compact configuration
- Customised and application-specific configurations and technical solutions
- Systems for detecting product contamination and rejection in terms of integrated quality assurance
- Intelligent palletising solutions
ContiFlex Bottle Packer
Process up to 60 packs per minute with the A+F ContiFlex bottle packer. You want high format flexibility for the carton line? Our bottle packer enables really easy handling of open trays, wrap-around trays, trays with shoulder tabs or shoulder trays – and with an output-oriented product infeed and the option of connecting several filling lines. With its servomotor-driven movement, an integrated suction cup module with line tracking as well as the configuration for the wet area you can use this machine in dairies, in the food and beverage industry, and in many other sectors.
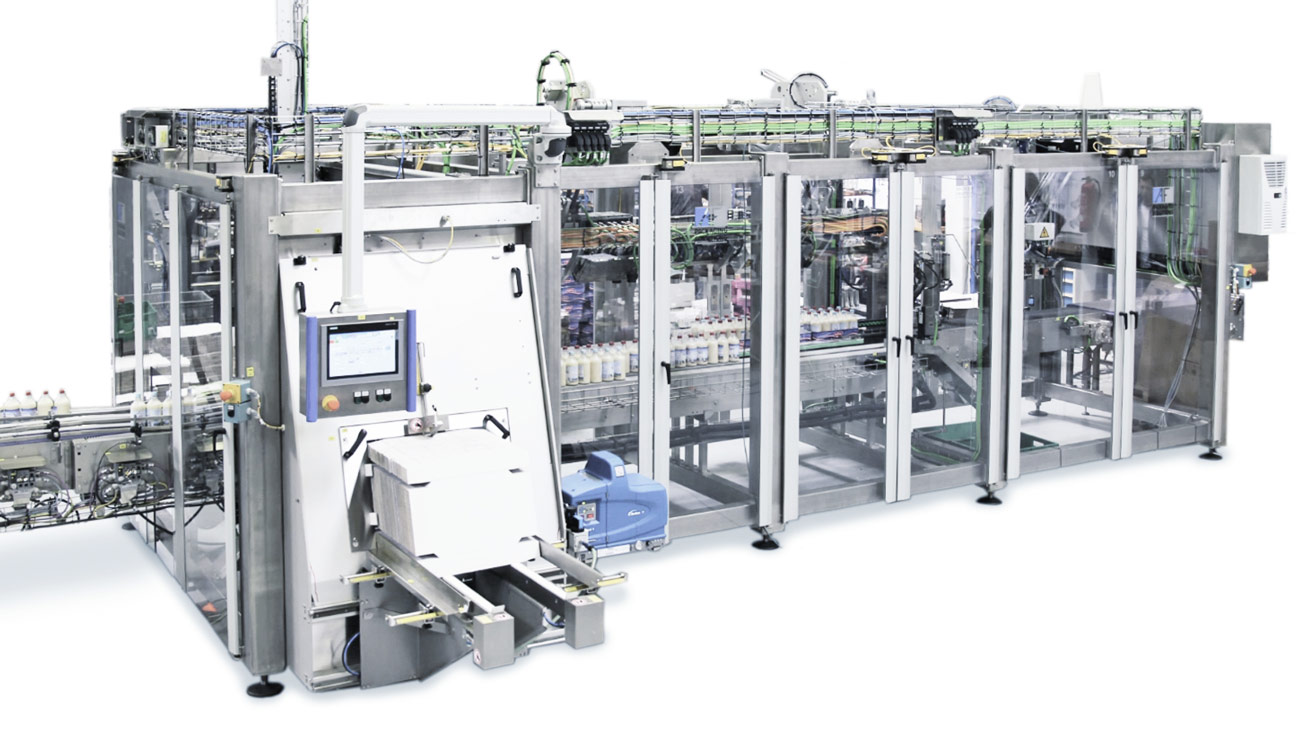
A+F ContiFlex in detail
Benefits
- High output of up to 60 packs/minute and performance-based product infeed with optional connection of multiple filling lines to the ContiLine
- High format flexibility of the case line enables processing of open trays, wrap-around trays, trays with shoulder flap or shoulder trays
- Easy cleaning with cleaning media due to division into working and drive levels with low production costs due to high-quality, low-maintenance design
- Ergonomic design for optimum operability and fast format changeover in less than 10 minutes
- Jamless and guideless infeed
Technical details
- Bottle type: Trays and wrap-around cartons, all standard market dimensions; 4- and 8-corner trays, various bottle shapes with bottle heights from 100 mm up to 222 mm without format parts / format changeover in the line
- Capacity: 15,000 bottles / hour
- Control: Schneider Electric
Schneider Electric servo motors with planetary gear or angular gear
SEW rotary motors
HMI Siemens TP 1200 Comfort
Applications
- Trays
- Wrap-Around trays
- in all customary heights and shapes
Options
- Connection to upstream and downstream systems
- Customised and application-specific configurations and technical solutions
- Marking systems
- Systems for the detection of product contamination and rejection in terms of integrated quality assurance.
- Intelligent palletising solutions